Can metallurgy be considered a sustainable environmental technology? This is the question that bothers not only environmental activists, but anybody concerned with the mining industry having a considerable impact on the natural environment. Be that as it may, let‘s start from the beginning – what is a sustainable environmental technology?
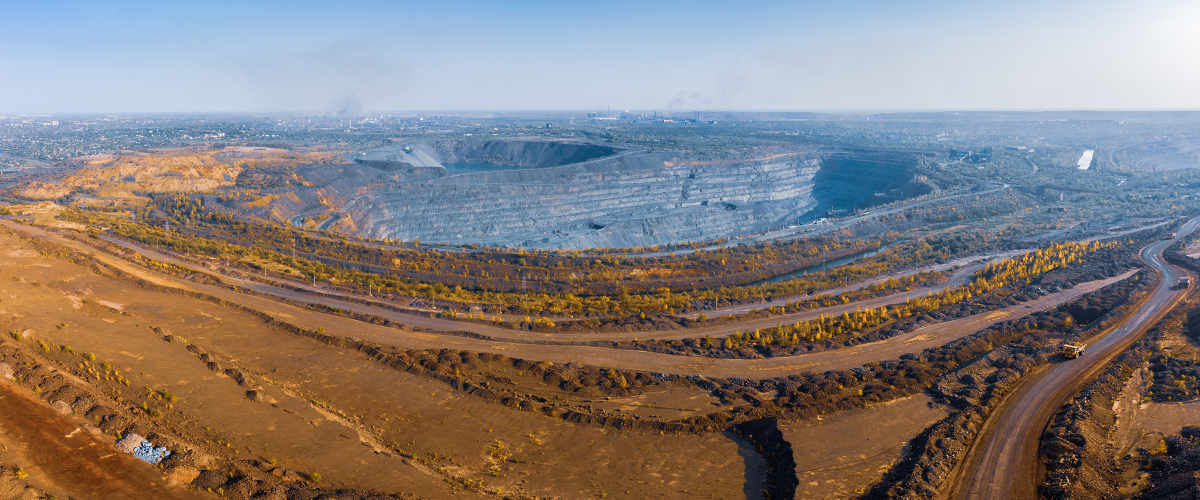
According to European Commission‘s definition – it‘s a technology, which – comparing with other, similar technologies – bears a competitive advantage of being the least damaging to the natural environment. But let‘s facet it – mining natural resources and refining the extracted ores can hardly be considered as having a low environmental impact.
Of course, regular consumer has little to none impact on preventing devastation of the natural environment by the mining industry, yet we have a choice – understanding how the processes work, and the way technological mechanisms are applied, how to treat waste and scrap materials – this knowledge can influence our buying habits. It‘s on us who we choose as a supplier – and avoiding large polluters will cause market mechanisms do the job for us. Manufacturers will have the choice – either adjust their approach to the natural environment and change business models, introduce environmental measures and stay in business; or face bankruptcy, with enormous penalties and sanctions for disobeying international environment-related laws.
Sustainable development is based on three main pillars – society, natural environment and economy, and these are fueled by efficient energy sources, proper scrap management and efficient production process. Let’s look at some metals and how they are mined, refined, used to produce the final product and at the end of the product life span, how they are recycled. We hope that provided information will help you understand how a conscientious purchasing habits influence impact on environment and the future of our planet.
Tantalum is a key material in the electronics industry, mainly because of its use in condensers. It is estimated that 40% of global tantalum production is used in this application, yet surprisingly only 1% of tantalum is recycled. Taking into consideration that electronic waste is the fastest growing waste category worldwide, year after year the technology improves and metal recycling gets more efficient, there is hope for recycling a considerable amount of metals and other materials. It’s a good approach, as recycling is much more efficient than mining – from both perspectives – economical and environmental impact. Circular economy slowly grows into an economical paradigm, which should finally change the business approach of many entrepreneurs all over the world. Recycling makes 25-30% of a global tantalum production, which translates into 500 tons of tantalum each year. So, why is electronic waste so poorly recycled? The answer is quite simple – because of technology. A typical electronic device consists a similar amount of tantalum as in tantalum ore, however a printed circuit board also consists of other elements such as gold, palladium or copper – much more valuable than tantalum. These are recovered using pyrometallurgical methods, which turn tantalum into oxide (slug), hence making it economically unattractive. But is it always about economic gain?
There are two main sources of aluminum – primary, refined from bauxite and secondary, from recycling. Bauxite is a sedimentary rock, a main source of aluminum, consisting of 30 – 50 % of aluminum in form of oxide. Mining of bauxite requires drastic intervention into a natural environment – tree and vegetation removal, land use, water pollution and huge energy consumption. Taking into consideration, that such energy is obtained by combustion of fossil fuels – coal, oil and natural gas, the list of negative impact factors get longer and longer. It is estimated, that to produce 1 ton of bauxite, 150 MJ (or 41.6 kWh) of energy is needed, which makes production of bauxite one of the least energy consumptive branches of the mining industry. Sounds good? Wrong! Secondary aluminum, obtained from recycling requires only 5% of that energy. And energy saving is not the only advantage, as the emission of green house gases has similar proportions.
Contrary to common opinions, titanium is neither rare nor noble. Its high price is directly linked with refining process, a long, expensive and complex Kroll process requires a lot of energy. Titanium is six times more expensive to produce than steel! Kroll process is comprised of the following steps:- chlorination: during which titanium dioxide turns into TiCl4;
- reduction and separation: titanium tetrachloride is purified with magnesium to form metallic titanium sponge;
- melting: titanium sponge is crushed and melted in vacuum arc furnace;
- electrolysis: at this stage magnesium chloride is decomposed into magnesium and chlorine gas, which then are used again in the reduction and chlorination process.
Scrap out of technically pure titanium, with low content of impurities (mainly oxygen and iron) are re-melted and used again, while titanium scrap with high amount of impurities (ferrotitanium – with titanium content up to 75%) is mostly used for denitrogenation and deoxidizing process in steel production. Reused and remelted titanium doesn’t require refining – which is very ecologically advantageous. Let’s promote titanium recycling!
Nickel, as always, steps out of line. Constantly growing demand for this metal, requires continual need to expand the mining sites. This makes secondary production even more important. Nickel can be infinitely recycled without loss of quality – which makes it the most recycled metal with the recycling rate at 68%. Majority of the recovered nickel is used for stainless steel production.
Metal refining and its impact on the natural environment is only a part of the picture. Also the mining industry plays a gigantic role in environment devastation. Slag heaps (waste rock disposal) are located in the nearby location to the mine, to cut the costs on haulage. Such heaps contain sulphide minerals, which eventually gets released into stream waters. Such emissions precipitate creating acidic conditions and as a result killing all vegetation in the area.
Let’s actively promote material recycling, it’s cheap, easy and most importantly – will pay off in the future. Our children and grand children will thank us later!
Source: https://www.worldcat.org/title/handbook-of-extractive-metallurgy/oclc/1184141499Other articles
Norms and standards of non-ferrous metal products
All non-ferrous metal products offered by WOLFTEN are manufactured according to specific standards. Clearly defined technical standards guarantee the homogeneity of the materials used, which directly affects the specific characteristics of each structure and their safety.
Neural networks in metallurgy
Ability to develop, create and apply a specific material marks the border between business success or failure. Forecasting mechanical properties of a new alloy is an important aspect for both scientists and engineers as it allows saving time and money.
Corrosion
What is corrosion? From the chemical point of view, it is a natural, electrochemical process between the surface and the environment, converting a refined metal into a more stable form of oxides, hydroxides or sulfides.