Każdy ją zna i w większym lub mniejszym stopniu miał z nią do czynienia. Gdyby nie korozja obecna gospodarka światowa wyglądałaby zupełnie inaczej – wystarczy sobie wyobrazić przemysł lub transport, którego nie dotyka problem korozji. Nasze samochody nie musiałyby być zabezpieczane lub całe ich części nie wymagałyby regularnych wymian. Urządzenia codziennego użytku służyłyby wiele lat bez awarii, nie doszłoby do wielu katastrof ekologicznych, których sztandarowym przykładem była katastrofa tankowca Erika u wybrzeży Bretanii w 1999 roku. Przemysł hutniczy byłby znacznie uszczuplony, a w urządzeniach elektrycznych wykorzystywanoby o wiele więcej miedzi niż obecnie.
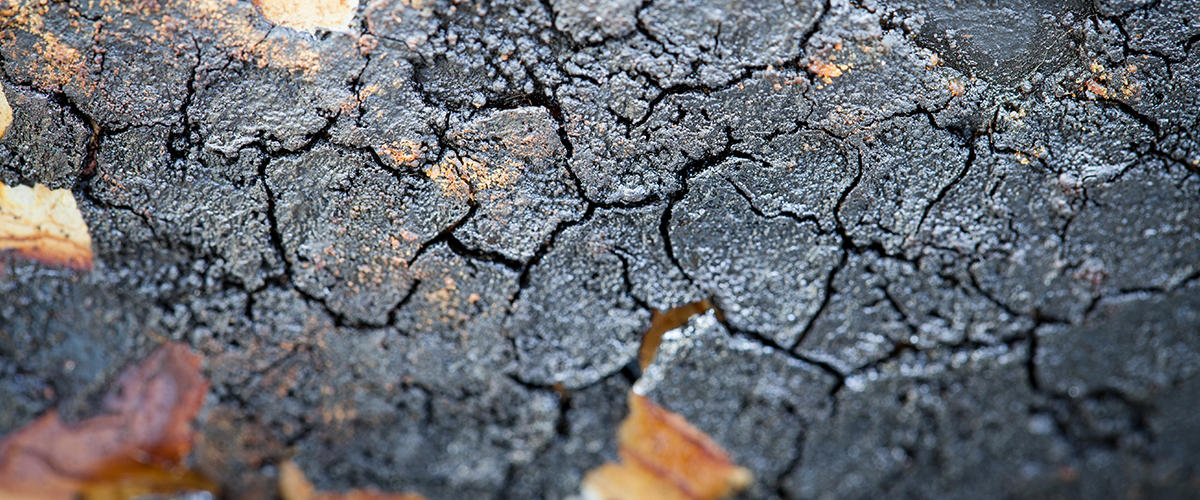
Według raportu NACE International globalne straty związane z korozją materiałową szacowane są co roku na kwotę 2,5 biliona (2 500 000 000 000) USD, co czyni około 3,5% całoświatowego PKB. O ile kwota robi olbrzymie wrażenie, to niestety ta swoista „choroba materiałów„, zgodnie z zasadami termodynamiki, nie może być zatrzymana, trwa bez przerwy, a wysiłki ekspertów od metalurgii skupiają się jedynie na spowolnieniu jej postępowania. Dzięki zastosowaniu środków ochrony antykorozyjnej straty można obniżyć o 15 – 35%, co daje niesamowitą kwotę od 375 do 875 miliardów USD rocznie w skali całego świata. Nie zmienia to faktu, że w tych niewyobrażalnych sumach nie zawiera się kosztów związanych z zanieczyszczeniem środowiska – m.in. wspomniana powyżej katastrofa tankowca Erika, podczas której do wód Atlantyku wydostało się tysiące ton ropy, a obszar skażenia wynosił ponad 28 tysięcy kilometrów kwadratowych, dla wielu z nas jest nie do oszacowania, właśnie ze względu na ogrom zanieczyszczenia.
Czym więc jest ten niewidzialny potwór, któremu niestraszne są nawet najtwardsze materiały? W przypadku metali można go zdefiniować jako proces chemiczny lub elektrochemiczny zachodzący pomiędzy powierzchnią a otaczającym środowiskiem, związany z naturalnym zjawiskiem zmiany, podczas której metal rafinowany powoli przyjmuje bardziej stabilną chemicznie formę tlenków, wodorotlenków lub siarczków.
Pewnym wyjątkiem są tu jednak metale szlachetne – platynowce (ruten, rod, pallad, osm, iryd oraz platyna) oraz złoto i srebro. Metale te bardzo słabo reagują z innymi pierwiastkami, prawie nie ulegają korozji a w środowisku naturalnym mogą występować w tzw. postaci rodzimej.
Aby podjąć jak najskuteczniejszą walkę z wszystkożerną bestią należy ją dokładnie poznać, dlatego zjawisko korozji zostało podzielone na wiele podgrup oraz rodzajów.
Korozja atmosferyczna (ang. Atmospheric Corrosion) jest chyba najbardziej przebadaną formą korozji, a na jej temat powstało wiele publikacji naukowych, poczynając od prac E. Wilsona, który na początku XX wieku opisał swoje obserwacje zmian zachodzących na powierzchni przewodów elektrycznych w Londynie. Korozję atmosferyczną wywołuje powietrze oraz zawarte w nim zanieczyszczenia, a jej szybkość postępowania uzależniona jest od ilości elektrolitu. Takim elektrolitem może być deszcz, rosa lub ogólnie wilgoć zawarta w powietrzu – ze względu na to, że woda jest uniwersalnym rozpuszczalnikiem, oraz zawarte w niej chlorki oraz dwutlenek siarki. Chlorki zazwyczaj pochodzą z wody morskiej lub soli drogowej używanej do odladzania dróg, natomiast dwutlenek siarki pojawia się jako produkt spalania paliw kopalnianych, np. węgla (ponownie pojawia się kwestia zanieczyszczenia środowiska naturalnego).
Korozja atmosferyczna jest najczęstszą przyczyną degradacji elementów metalowych, co odzwierciedla fakt, że na zabezpieczenia materiałów przeciw korozji atmosferycznej wydaje się 50% wszystkich kosztów zabezpieczeń antykorozyjnych. Nie ma się co dziwić, bo żaden inny rodzaj korozji nie ma tak destruktywnego wpływu na materiał – ulegają jej zarówno małe elementy, jak i wielkie architektoniczne megastruktury, takie jak drapacze chmur lub mosty.
Tytan ulega pasywacji, spontanicznie tworząc na swojej powierzchni warstwę dwutlenku tytanu, która skutecznie chroni przed korozją w środowisku naturalnym.
Korozja elektrochemiczna (Galvanic Corrosion) jest korozją występującą lokalnie w okolicach miejsc kontaktu dwóch metali. Im dalej od miejsca kontaktu, tym intensywność występowania korozji gwałtownie maleje.
Ten typ korozji jest wywoływany różnymi procesami elektrochemicznymi (prawdopodobnie stąd nazwa 😉 ). Procesy te zachodzą dzięki występowaniu różnic w potencjałach pomiędzy fragmentami stykających się metali o różnych składach chemicznych, tworzą się tzw. ogniwa galwaniczne (lub ogniwa korozyjne). Stop o niższym potencjale przyjmuje rolę anody, ten o wyższym – katody, a elektrolit, który wykazuje przewodnictwo jonowe, ułatwia przemieszczenie się elektronów pomiędzy nimi, przyspieszając proces utleniania anody.
Korozja elektrochemiczna ma jednak pewne zastosowania – do produkcji czujników wilgoci oraz do pewnych zastosowań militarnych, m.in. do produkcji bezpłomieniowych podgrzewaczy chemicznych, polegających na wywołaniu reakcji elektrochemicznej pomiędzy proszkami magnezu oraz żelaza. Zjawisko korozji elektrochemicznej wykorzystywane jest również w większości baterii, które zasilają urządzenia elektroniczne codziennego użytku.
Kontakt tytanu z innym metalem nie wywołuje zwiększonej korozji tego pierwszego. W większości wypadków tytan przyjmuje rolę katody, co powoduje powstanie cienkiej warstwy pasywnej zbudowanej z wodorków tytanu, która generalnie jest stabilna i nie stwarza żadnych problemów. Wyjątkiem jednak są środowiska redukujące, w których tytan nie ulega pasywacji i, podobnie jak aluminium, w przypadku połączeń z bardziej szlachetnymi metalami, wykazuje zwiększoną skłonność do korozji.
Korozja wżerowa (Pitting Corrosion) polega na tworzeniu się miejscowych zagłębień (wżerów) na powierzchni materiału. Narażone na nią są metale, które w normalnych warunkach ulegają pasywacji (tworzenie się warstwy tlenku na powierzchni). Wszelkiego rodzaju uszkodzenia mechaniczne powierzchni, niedoskonałości w strukturze lub działania chlorków mogą doprowadzić do przerwania warstwy pasywnej, co spowoduje tworzenie się zagłębień. Dno takich zagłębień staje się anodą, a reszta powierzchni przyjmuje rolę katody, coraz bardziej pogłębiając wżer. Korozja wżerowa jest niebezpieczna przede wszystkim dlatego, że jest trudna do wykrycia. Dodatkowo, powstanie pojedynczego wżeru w najbardziej newralgicznym punkcie może zagrozić stabilności całej konstrukcji. Do najbardziej znanych wypadków spowodowanych korozją wżerową była eksplozja systemów kanalizacyjnych w Guadalajarze, drugim co do wielkości mieście Meksyku.
Korozja wżerowa stopów tytanu w temperaturach otoczenia niższych niż 100°C występuje bardzo rzadko, aczkolwiek w przypadku środowiska skoncentrowanego chloru może nastąpić już w zakresie temperatur 100 – 200°C.
Korozja szczelinowa (Crevice Corrosion) jest rodzajem korozji elektrochemicznej powstającej w trudnodostępnych miejscach, np. na złączach różnych powierzchni przy połączeniach śrubowych lub nitach. Pojawia się zazwyczaj tam, gdzie znajdują się niewielkie resztki elektrolitu.
Korozja międzykrystaliczna (Intergranular Corrosion) występuje na granicy ziaren stopu, co znacznie wpływa na wytrzymałość, powodując jego pękanie i łamliwość. Jednym ze sposobów ochrony przed korozją jest dodawanie tytanu lub niobu jako elementu stopowego. Zarówno tytan, jak i niob są pierwiastkami silnie węglikotwórczymi, dzięki czemu zapobiegają zubożaniu chromu na powierzchni ziaren.
Korozja złuszczająca (Exfoliation Corrosion) to siostra korozji międzykrystalicznej, która tworzy się na granicach ziaren, wzdłuż powierzchni, wytwarzając odrywające się warstwy przypominające w swej strukturze ciasto francuskie. Stopy aluminium są w szczególności podatne na ten rodzaj korozji. W jaki sposób można się przed nią zabezpieczyć? Najlepiej poprzez stosowanie powłok zabezpieczających lub odpowiednią obróbkę cieplną stopu, np. utwardzanie wydzieleniowe.
Pękanie pod wpływem korozji naprężeniowej (Stress Corrosion Cracking) to takie pękanie materiału, na które składają się dwa jednocześnie występujące elementy: czynnik korodotwórczy oraz oddziaływanie stałego naprężenia mechanicznego. Zjawisko to występuje ze względu na fakt, że pod wpływem naprężeń powierzchna nie jest jednorodna energetycznie.
Korozja nitkowa (Filiform Corrosion) jest szczególną formą korozji, która występuje pod powierzchnią powłoki przyjmując formę losowo rozchodzących się nitek. Najczęściej występuje na powierzchni z powłokami o grubości około 1 mm. Owe nitki nie są niczym innym, niż tunelami powstającymi pomiędzy powierzchnią a powłoką wytworzonymi przez produkty korozji. Elektrolit przedostaje się do kontaktu z powierzchnią metalu w wyniku osmozy wywołanej dużą ilością jonów żelaza.
Korozja mikrobiologiczna (Microbiologically Induced Corrosion) jest wywołana obecnością lub działaniem mikroorganizmów, bakterii beztlenowych, które w procesie metabolicznym przeprowadzają redukcję siarczanów lub innych związków siarki.
Jest jeszcze Corrosion of Conformity, ale to już zupełnie inna historia….
Pozostałe wpisy
Nikiel a zielona rewolucja energetyczna
Mimo że zdecydowana większość globalnego wydobycia niklu, bo aż ok. 80%, wykorzystywana jest do wytwarzania stali, metal ten jest także niezbędnym ogniwem dla zielonej energetycznej rewolucji i pozyskiwania eko energii na miarę XXI wieku.
Normy i standardy materiałowe
Wszystkie produkty z metali nieżelaznych w ofercie naszej firmy są wykonane według określonych norm. Doprecyzowane standardy techniczne są gwarancją jednorodności stosowanych materiałów, co przekłada się na właściwości konstrukcji.
Zrównoważone technologie środowiskowe a metalurgia
Idea zrównoważonego rozwoju jest coraz szerzej uwzględniana w rozwoju gospodarczym i działaniu firm z wielu sektorów przemysłu. Nacisk na ochronę środowiska i konieczność wprowadzenia zmian podnoszone są już nie tylko przez aktywistów środowiskowych. Świadomość...